What is Aluminum Anodizing?
Aluminum anodizing is an electrochemical process that transforms the surface of aluminum into a durable, corrosion-resistant, and visually appealing finish. The process involves immersing the aluminum in an electrolytic bath and applying an electrical current. This causes an oxide layer to form on the aluminum’s surface, which can be customized in terms of thickness and appearance. This film layer enhances the surface hardness, wear resistance, and other functional properties of the metal.
Anodizing diagram
The anodic oxidation surface is AL2O3 oxidized layer, which is applicable for the products of plane veneering and light bending.
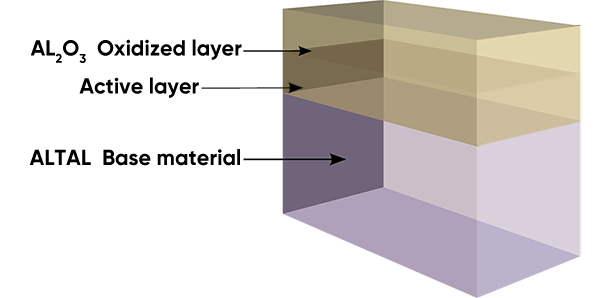
Why Anodizing
To address the limitations of surface hardness and wear resistance in aluminum alloys and broaden their applications while prolonging their service life, surface treatment technologies have become crucial. Among these technologies, anodizing is the most widely adopted and successful method.
Aluminum Anodizing Principle
A metal or alloy part is used as an anode to form an oxide film on its surface by electrolysis. The metal oxide film changes the surface state and properties, such as surface coloring, corrosion resistance, wear resistance, hardness, and protection of the metal surface. For example, in aluminum anodizing, aluminum and its alloy are placed in the corresponding electrolyte (such as sulfuric acid, chromic acid, oxalic acid, etc.) as an anode and electrolyzed under specific conditions and current. The anodized aluminum or its alloy is oxidized to form a thin layer of aluminum oxide on the surface, with a general thickness of 3 to 10 μm for interior decorative films and 15 to 25 μm for exterior films, and up to 40 to 200 μm for hard anodized films.
The anodized aluminum or its alloy improves its hardness and wear resistance up to 220-500 kg/mm2, good heat resistance, hard anodized film melting point up to 2300K, excellent insulation, breakdown voltage up to 2000V, enhanced corrosion resistance, in ω = 0.03 NaCl salt spray after several thousand hours without corrosion. The thin layer of oxide film has a large number of microporous, can adsorb a variety of lubricants, suitable for manufacturing engine cylinders or other wear-resistant parts; film microporous adsorption capacity can be colored into a variety of beautiful and bright colors.
Non-ferrous metals or alloys (such as aluminum, magnesium and alloys, etc.) can be anodized, and this method is widely used in mechanical parts, aircraft and automobile parts, precision instruments and radio equipment, daily necessities and architectural decoration, etc.
Process of Anodizing
Degreasing→Etching→Neutralizing→Anodizing→Colouring→Sealing
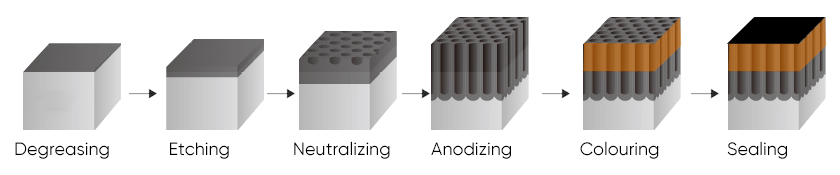
Functions of Anodized Aluminum
1. Protective:
The primary function of anodizing is to create a protective barrier on the aluminum surface. The anodized layer acts as a shield against corrosion, preventing the aluminum from rusting and deteriorating even in harsh environments.
2. Decorative:
Anodizing allows for a wide variety of colors and finishes, making it a popular choice for decorative applications. It enhances the visual appeal of products, from architectural elements to consumer electronics.
3. Insulation:
The anodized layer can serve as an electrical insulator, which is valuable in electronic goods where insulation is essential for safety and performance.
4. Improves Adhesion to Organic Coatings:
Anodized aluminum provides an excellent surface for adhesion, making it easier for organic coatings like paint to adhere, ensuring durability and long-lasting finishes.
5. Improves Adhesion to Inorganic Coatings:
Inorganic coatings, such as ceramic or PTFE, bond exceptionally well with anodized aluminum, further enhancing its versatility in various applications.
Features of Anodized Aluminum
1. Lightweight:
Aluminum is naturally lightweight, and anodizing does not add significant weight to the material. This makes anodized aluminum an ideal choice for applications where weight is a critical factor, as it weighs only one-third of stainless steel.
2. High Tensile Strength:
Anodized aluminum exhibits impressive tensile strength, approximately 2.5 times that of ordinary aluminum sheets, providing enhanced structural integrity.
3. Excellent Corrosion Resistance:
The anodized layer increases aluminum’s corrosion resistance, making it three times more resilient than untreated aluminum and twice as resistant as stainless steel.
4. Aesthetic Options:
Anodizing offers a spectrum of colors and finishes, allowing for diverse and beautiful surface treatments that can be tailored to specific aesthetic requirements, making it ideal for architectural applications.
5. Flexibility:
Anodized aluminum is highly malleable and can be easily cut into various shapes and sizes, making it a versatile choice for roofing, wall cladding, and more.
6. Environmental Friendliness:
Anodized aluminum is environmentally friendly with a service life of more than 50 years and is 100% recyclable, making it a sustainable choice for eco-conscious applications.
7. Noise Reduction and Shock Absorption:
Anodized aluminum has noise-reduction and shock-absorption properties, making it ideal for applications where it needs to withstand impact loads.
Applications of Anodized Aluminum
1. Architecture
Anodized aluminum sheets have become an architect’s choice due to their corrosion resistance, durability, and ability to withstand harsh weather conditions. They are used in interior wall, ceiling, and decorative elements, offering both structural support and aesthetic appeal. The material’s lightweight nature also makes it convenient for architectural designs that prioritize both aesthetics and functionality.
In the realm of household appliances, anodized aluminum sheets are valued for their resistance to corrosion, heat, and scratches. They are employed in manufacturing kitchen appliances like cookware, refrigerators, and ovens, where durability and a sleek finish are essential. The material’s ability to withstand frequent use while maintaining an attractive appearance contributes to its popularity in this sector.
3. Automotive
The automotive industry benefits from anodized aluminum sheets due to their lightweight yet robust properties. These sheets are utilized in car body panels, trim components, and interior decorative elements, providing both structural integrity and a polished finish. The material’s ability to enhance fuel efficiency due to its lightweight nature has made it a valuable choice for manufacturers seeking to improve vehicle performance.
Anodized aluminum sheets are prevalent in the electronics industry, where they are used in the production of casings for devices such as laptops, smartphones, and tablets. Their ability to dissipate heat efficiently, along with their electrical conductivity, makes them ideal for ensuring the proper functioning and longevity of electronic gadgets.
5. Crafts
Aluminum anodizing is used in crafting and jewelry making to create colorful and corrosion-resistant aluminum pieces. The process allows for a wide range of color options, making it popular for artistic and decorative applications.
Anodized aluminum sheets find their way into various other applications, including suitcase exteriors, socket and switch panels, closet doors, signage, and packing materials. The material’s resistance to abrasion, weather, and corrosion ensures its suitability for diverse purposes, where both durability and aesthetics play crucial roles.