Nowadays, anodized aluminum sheets are the most popular choice for architectural decoration and 80% of them are in their natural silver color.
Why not use color anodized aluminum sheet? What’s the reason?
There is a case, many years ago, a construction unit purchased gold anodized aluminum sheets for exterior wall decoration. After a month, the color faded, completely different from the previous comparison. Eventually, the construction unit had to demolish and rebuild the building.
Why would this happened?
First, we need to know that there are two methods for coloring anodized aluminum sheet.
1. Using organic dye to color
This dye is not resistant to light. It can be used indoors without direct sunlight, but if used outdoors, it will change color in a few days. The previous case is the use of dye coloring process, so it leads to quality problems.
2. Using electrolytic deposition process to color
This is the only coloring method that can meet the outdoor use requirements. However, anodized aluminum sheets that undergo this electrolytic coloring process have a shortcoming: the oxide film will crack after bending. This is the characteristic of anodized film, bending position dew white, especially colored anodized aluminum sheet. That’s why owners and builders don’t accept it.
Is there a solution that can meet the design requirements for both appearance and sheet metal processing?
Is there a solution that can meet the design requirements for both appearance and sheet metal processing?
Yes, there is! To address this problem, Altal has developed a new generation of outdoor color anodized aluminum sheet —Anodized Plated Aluminum Sheet. It uses anodized coating technology, the principle of which is to use ion deposition coating technology to color and seal holes after anodizing the aluminum sheet. This satisfies people’s demand for innovative decorative materials.
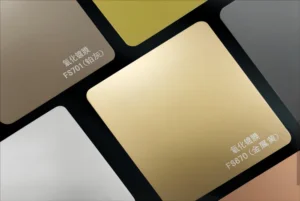