Our customers often ask: What makes Altal’s anodized aluminum sheets better than similar products available in the market, particularly in terms of performance, such as weather resistance?
Recently, a customer sent us a remarkably inexpensive anodized aluminum sheet. Upon careful inspection, we discovered residual fingerprints on the surface that could not be cleaned. What is the reason for this? Will it affect its use?
Usually, following the coloring and anodizing phases, a vital final step emerges — sealing. Anodizing aluminum involves an electrolytic oxidation process, transforming the surface of aluminum into an anodized film, followed by dyeing or electrolytic coloring, and ultimately, sealing. This sealing process plays a critical role in preserving color integrity while enhancing insulation, scratch resistance, abrasion resistance, corrosion resistance, and oxidation resistance. Poor sealing leads to surface imperfections like residual fingerprints, significantly reducing corrosion resistance and longevity of an anodized aluminum sheet.
What is the sealing process of anodizing?
The quality of an anodized aluminum sheet depends on the excellence of its sealing treatment. This process profoundly impacts its properties, including abrasion resistance, corrosion resistance, gloss, and color retention. In contrast to other companies that perform a single sealing, Altal’s anodized aluminum sheets undergo dual sealing, significantly enhancing their weatherability,, scratch resistance, and lifespan.
During the production of aluminum anodizing, the anode often develops a porous structure due to the influence of power supply polarity. This structure possesses high surface activity, making it susceptible to pollutants and corrosive substances. Additionally, colored pigments within the internal layer may easily leach out, diminishing the performance of the anodized film’s surface.
Therefore, sealing immediately after anodizing becomes imperative. The sealing process augments pollution resistance, corrosion resistance, abrasion resistance, and light resistance of the anodized film, ensuring the stability of the anodized aluminum sheet.
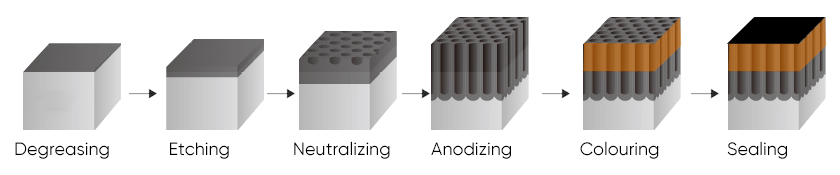
The Significance of Sealing
Sealing emerges as the vital step that confers protective properties upon the anodized film. It involves sealing the porous structure within the anodized layer after anodizing. By sealing the honeycomb pores generated during the electrolysis process, the anodized film gains crucial protective value. Otherwise, owing to its strong adsorption capacity, pollutants and corrosive substances might be easily absorbed. Consequently, an unsealed or inadequately sealed anodized film may exhibit inferior corrosion resistance compared to a natural oxide film.
Assessing Sealing Quality
A fundamental method to evaluate the quality of the anodized film layer is the weight loss test. A lower weight loss value signifies diminished quality loss and superior sealing. The national standard (GB/T 23443) specifies that a weight loss not exceeding 30mg/dm2 is deemed acceptable for adequate quality. Regardless, the sealing process in anodizing remains an indispensable stage.